No new solution for electric vehicle (EV) batteries has been commercialized since the advent of lithium-ion batteries in the 1990s. Since then, the EV market has exploded from less than 5% of market share in 2020 to 14% in 2022. It’s projected to increase to 18% by the end of 2023, and to 60% by 2030. But while lithium-ion EV batteries have significantly improved since the first modern EV was released, concerns remain about their driving range, cost, charge time and safety.
These issues have led manufacturers to seek a more powerful, safer battery technology for the next generation of EVs. As demand and incentives for electrified vehicles increase along with stricter emissions regulations, solid-state battery prototypes have produced promising results to help address the automakers concerns.
However, the path from prototype to full-scale battery commercialization can be long and arduous. We believe it is crucial for battery developers and OEMs to partner on developing and scaling cost-effective solid-state batteries to power a clean, sustainable, and cost-effective electrified future.
Why Commercialize Solid-State Batteries?
While the market for EV’s is booming, the limitations of using conventional liquid lithium-ion batteries still cause many potential EV owners to hesitate before purchasing one. Common concerns include these batteries’ fire safety and limited range on a single charge. Solid-state batteries (SSB) have the potential to mitigate these issues and increase prospective customers’ confidence in buying safe, reliable EVs while improving EV sustainability.
Increased Driving Range
On average, current EV batteries provide only half the driving range per charge that an equivalent gas vehicle gets per tank. In an effort to resolve drivers’ concerns about being stranded, the Factorial Electrolyte System Technology (FEST®) battery uses a conventional cathode chemistry combined with a lithium-metal anode and Factorial’s propriety quasi-solid electrolyte, which can enable a 20-50 percent higher energy density increase over today’s lithium-ion batteries.
Factorial Energy’s FEST® technology has the potential to revolutionize EV batteries with enhanced safety and range, while leveraging existing lithium-ion battery production processes and equipment.
Factorial’s batteries’ ability to pack more power and energy into the available battery packaging space has the potential to give EVs a substantially longer driving range per charge than existing EVs, allowing customers to get the economic and environmental benefits of EVs without having to sacrifice their driving range. These more energy dense batteries also reduce the battery’s weight, further increasing EV efficiency and impact on the roads.
Safer and Less Flammable
The highly flammable liquid electrolytes in conventional lithium-ion batteries have led to highly publicized instances of EVs catching fire. The organic liquids are typically volatile between 60-75 degrees Celsius. Long-term exposure to 50°C temperatures can degrade the cells’ performance, shorten their lifespan, and lead to a catastrophic thermal incident if the heat is not dissipated.
In contrast, FEST® quasi-solid electrolytes have been shown to remain stable up to 200 degrees Celsius (from the Differential Scanning Calorimetry (DSC) data). This stability has shown significantly lower risk of fires and cell degradation from high temperatures, giving the OEMs and EV owners more peace of mind and an overall lower cost of ownership for the vehicle.
How Close Are We to Solid-State Battery Commercialization?
Currently, all solid-state battery cells are in the development process and not yet available on the mass market. We believe our FEST® battery system is ahead of many solid-state battery concepts in that we have developed a working 100+Ah A Sample prototype. In fact, Factorial just announced their large format Lithium-metal solid-state battery achieved UN 38.3 certification. This standard represents a requirement for the safe shipment of Li-ion and Li-Metal batteries and gives us the green light to ship our 100+Ah cell to customers.
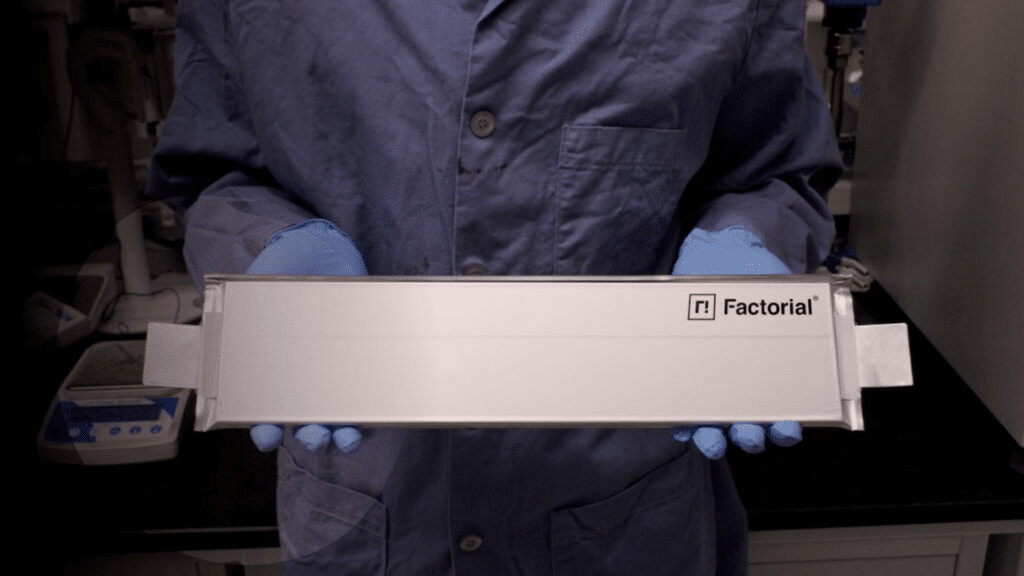
Factorial Energy’s 100+Ah Li-metal solid-state battery preview
The A, B, C, D’s of EV Battery Testing
Original equipment manufacturers (OEMs) follow a clear commercial roadmap when bringing new technology to the automotive market. This rigorous and lengthy process is designed to ensure that customers can rely on the performance of every component of their vehicles, including EV batteries:
Research and Development (R&D)
Research and development teams test the science behind a new idea. In battery development, these teams often use tiny coin cells in laboratory conditions to test proof of concept.
R&D tests often reveal that the proposed technology is impractical or non-beneficial, so very few proceed to the next stage. Factorial’s FEST® battery is one of the few which has passed R&D testing, showing both proof of concept and significant benefits over existing technologies.
A Sample Testing: Real-World Validation
The manufacturer creates several production intent batteries within a production representative cell format and capacity, and tests them in laboratories and in some cases real-world conditions to indicate their safety, performance, and functionality. Cell technologies that pass A-validation testing are considered to move to the next development phase or changes are made and A-Sample validation restarts.
Sample B Testing: Design Validation
The next batch of prototype batteries is tested part-to-part at the cell and module level to optimize the batteries’ design and verify their performance in packs and vehicles. Manufacturers and the battery partner can agree to freeze the batteries’ physical design and chemistry and then move to the next phase of development.
Sample C and D Testing: At-Scale Production Validation
With the cell design and materials frozen, battery manufacturers now begin the process of scaling production to develop a stable process with consistent high-quality results. Passing Sample C and D validation certifies the batteries can be produced at reliable production volume and quality.
Full-Scale Production
Having completed the final Production Process and Product Approval phase (PPAP) in the C/D phase, the battery production line is verified to be running at rate with a finalized process and quality control plans in place. Those are the cells that ultimately end up in a consumer product like an EV.
How to Make Solid-State Batteries Scalable and Affordable
Every step of the testing and development process can take several years for the battery to meet rigorous industry standards, guidelines, and regulations from authorities including the International Electrotechnical Commission and the U.N. During the development process, companies are limited to small-scale production and have to establish a new supply chain and manufacturing infrastructures. These requirements and challenges have slowed the development of solid-state batteries – but with the right technology, the right policies, and the right partnerships, they don’t have to.
We’re also excited to see national and international governments adopt policies that allocate funding to emerging EV battery technologies. The United States’ Inflation Reduction Act provides loans and grants to EV battery makers in the U.S. Additionally, new EPA emissions regulations and the European Commission’s proposed new regulations, such as the Battery Passport and Green Deal initiatives (which aim to make Europe the world’s first climate-neutral continent by 2050), will also incentivize EV adoption. Our recent expansion to Germany allows us to be on the ground as these initiatives unfold, and collaborate with leading industry players to help accelerate the EV transition.
Because start-up battery companies cannot do this on their own, we believe the future of battery technology will rely most of all on successful collaboration all along the supply chain between OEMs, automotive manufacturers, and technology developers. For instance, Hyundai Motor Co., Stellantis, and Mercedes-Benz have invested in our FEST® platform. These partnerships garner not only investment but invaluable support organizationally, and open up access to their supply chains as we work towards validating our technology at the cell and module levels.
The growing number of EV technology investments by OEMs forms the basis for solid-state battery developers and manufacturers to overcome current challenges of scalability and cost-effectiveness. This will enable them to take advantage of the exponentially growing market for EV batteries. Valued at $56.4 billion in 2022, this market is projected to reach $134.6 billion by 2027 – a boon for OEMs that may help provide superior solid-state solutions.
Powering Progress with Solid-State Battery Commercialization
Commercializing solid-state batteries requires innovation, collaboration, and perseverance. We’re eager to realize the potential of reliable, powerful, affordable solid-state batteries to potentially transform the EV industry. With continued investment and innovation alongside our top-tier automotive partners, we believe the future solid-state batteries will fast-track a new norm of clean, sustainable, electrified transportation. Soon, charging your car before bed will be as mainstream as charging your phone today.